User:Debra Tabron/sandbox
Related Article(s):
CONTRIBUTOR(S): Gaisheng Liu and Jim Butler
Key Resource(s):
- Hydrogeological Methods for Estimation of Spatial Variations in Hydraulic Conductivity[1]
- Hydraulic conductivity profiling with direct push methods[2]
- Groundwater[3]
Introduction
Hydraulic conductivity is mathematically defined as the parameter K in Darcy’s Law[4] (see Fig. 1),
where: | |
Q | is the flow rate across area A of a porous medium, |
K | is the hydraulic conductivity, and |
i | is the hydraulic gradient, which can be computed as: |
where: | |
h1 and h2 | are the hydraulic heads at the ends of the experimental domain, and |
L | is the total length. |
Hydraulic conductivity is dependent on the properties of both water and the porous medium,
where: | |
k | is the intrinsic permeability of the medium, a parameter which is solely dependent on the geometry of the interconnected pores, |
g | is the gravitational constant, |
ρ | is the density of the pore water, and |
μ | is the dynamic viscosity of the pore water, respectively. |
Many approaches have been developed to characterize K[1]. These approaches can be grouped into two general categories based on how the K estimates are obtained:
- hydraulic methods that involve water injection or extraction and the measurement of the induced pressure response, and
- indirect methods that rely on empirical correlations, often site-specific in nature, between K and other more readily evaluated formation properties (e.g., resistance to electric current).
Because hydraulic methods can be directly related to the mathematical definition of K through Darcy’s Law, K estimates obtained with those methods are generally considered to be more reliable than those obtained with indirect methods.
Other classifications of K characterization approaches are possible. For example, approaches can be divided into those based on data collected in the field and those based on measurements on core samples in the laboratory. In the latter case, there can be considerable uncertainty about how representative the core sample is of field conditions.
Field-based approaches can be further subdivided based on whether the measurement is conducted in the subsurface or on the surface. Subsurface measurements provide the most reliable information about K variations at the scale needed for environmental site investigations. Nearly all field-based hydraulic methods are performed in the subsurface and require either boreholes or direct push (DP) installations for extracting or injecting water and monitoring the induced head changes. Compared to methods that rely on existing wells, DP approaches can be applied essentially wherever K information is needed, thus greatly expanding the spatial coverage of K measurement in the field. DP approaches, however, are generally limited to use in relatively shallow (20-30 m from land surface) unconsolidated settings.
Field K measurements can also be performed on the land surface or in an aircraft. Most of these are geophysical approaches that involve measuring electrical, magnetic, or seismic properties of the formation and then transforming them into K estimates using empirical relations. The biggest advantage of surface or airborne approaches is their minimal site disturbance, as no subsurface boring is needed. However, the resolution that can be provided is limited, as the measurements are typically affected by conditions over a relatively large volume of the formation. Geophysical methods can also be performed in boreholes. Borehole geophysical methods can provide a much higher resolution description of K than surface-based methods.
The scale of measurement is an important factor to consider when assessing various approaches. For water-supply investigations, a single estimate of K averaged over a large volume of an aquifer will usually suffice; such an estimate is commonly obtained via pumping tests in a well[3]. For water-quality investigations, however, K estimates over a large measurement volume are often of limited value[5]. In that case, small-scale K measurements that provide information about local geological controls on groundwater flow and transport are usually required to obtain reliable predictions of contaminant behavior and to design effective remediation systems.
In this article, we focus on the approaches that can be used to obtain small-scale, localized measurements of K for environmental site investigations. Only the more commonly used approaches are discussed. Some other approaches, such as dipole flow tests[6][7], tracer tests[8], or hydraulic tomography[9][10] will not be discussed here.
Hydraulic Testing Approaches
Pumping Tests
The pumping test is the most common method for determining K over a relatively large volume of an aquifer in water-supply investigations[5]. During a typical test, the pumping rate is kept constant, although it can be varied in time to obtain better signal-to-noise ratios in the acquired data[11]. In the constant-rate approach, a well, preferably centrally located at the site, is pumped while induced head changes are monitored at that and nearby wells. The head changes, along with the pumping rate, can then be used to estimate aquifer parameters using different models of the well-aquifer configuration[12][13]. Pumping test analyses can be facilitated using software packages like AQTESOLV (Aquifer Test Solver), which has been developed for analyzing different types of aquifer tests[14].
Pumping tests are primarily performed to obtain large-scale volumetric averages of aquifer parameters as well as information about aquifer boundaries. However, one form of the pumping test, the step-drawdown test, is specifically directed at getting information about the efficiency of the pumping well. The K estimate from a pumping test is an average over a large volume of the formation and does not provide information at the scale of most relevance for issues involving contaminant transport (e.g., meters or less). Thus, pumping tests are less commonly employed for environmental site investigations[5].
Slug Tests
The slug test is one of the most common methods for determining K at the scale of relevance for environmental site investigations[15][5]. Slug tests are typically performed in existing wells at multiple horizontal and vertical locations across the site to characterize the spatial distribution of K values. However, slug tests can also be performed in temporary installations such as DP rods. In this approach, a near-instantaneous head change is applied in the well or DP rods and the subsequent head recovery is used to estimate K. The initial head change can be introduced using a solid object (slug), compressed gas (pneumatic system), or by the addition/removal of a certain amount of water[15]. The recovery data can be analyzed using different models of the well-formation configuration[14][15]. In contrast to pumping tests, slug tests provide a K estimate that is primarily a function of the materials in the vicinity of the screened interval of the test well. Slug test data analyses can be facilitated using software packages like AQTESOLV (Aquifer Test Solver), which has been developed for analyzing different test methods[14].
Although a slug test is very simple in principle, considerable care must be taken in all stages of a test[1][15][5]. Because test responses are highly sensitive to the materials immediately adjacent to the test well, that well must be appropriately developed before a test is performed. Otherwise, the K estimate can be biased by a low-K zone (skin) that can form during well construction. In high-K formations, the head recovery is rapid, and pneumatic methods are often used to minimize the time associated with test initiation. In addition, due to the relatively high flow velocity, the impact of pipe hydraulics on pressure readings should be considered when analyzing slug test data from high-K zones[16]. In low-K formations, slug tests can take an extremely long time to complete, although test time can be significantly reduced by decreasing the effective casing radius (portion of well in which the water level is changing)[15].
Slug tests can be configured to obtain information about vertical variations in K along the screened (open) interval of a well. Test intervals can be isolated with straddle packers, and slug tests performed within that isolated interval. The straddle packers can be incrementally moved along the screened interval of a well to characterize the vertical variation of K at a relatively high resolution. Using a two-packer tool (Fig. 2A), slug tests have been performed in a number of 0.25-m intervals in a well at the Geohydrologic Experimental and Monitoring Site (GEMS) in the Kansas River valley[1]. At each isolated interval, multiple tests are performed, initiated with different head changes, following recommended test guidelines[15][5]. An example data set is presented in Figure 2B. The multi-level slug test K estimates compare favorably with estimates obtained using other approaches (Fig. 3).
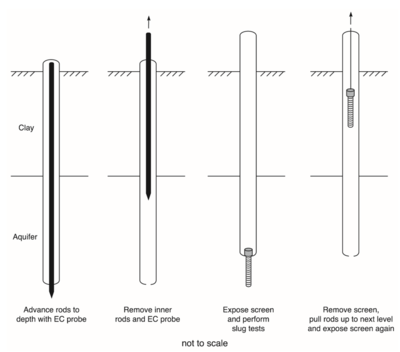
In addition to existing wells, slug tests can also be performed in DP installations so that K estimates can be obtained virtually at any location in unconsolidated formations. Various approaches have been developed that allow slug tests to be performed at one or multiple levels in a single DP hole[18][19][20][17]. In McCall et al. (2002)[20], a pair of nested rod strings were driven to the test interval with a solid drive point attached to the end of inner rod string for advancement. Upon reaching the test depth, the drive point and inner rod string were retracted, and a screen was lowered to the bottom of the outer rod string. The outer rod string was pulled up while the screen was held in place, leaving the screen exposed to the surrounding formation. After the slug test was completed in the exposed screen, the screen was removed and the inner rod string with the attached solid drive point was reinserted. The nested rod strings were then driven to the next test depth. In low-K formations such as silts and clays, the formation materials may not collapse completely back to the screen when the outer rod string is pulled up. In this case, the diameter of the borehole can be estimated and used in place of the screen diameter, or the problem can be avoided by using a coring tube of similar size to the screen to create a hole below the end of the outer rod string. Instead of setting the screen by pulling up the outer rod string, the screen can be directly inserted into the hole for slug testing. Regardless of how the screen is set into the formation, it is always recommended that the screen be appropriately developed before slug tests are performed. In low-K formations, development may be limited to scraping the sides of the cored hole with a steel brush and removing the silty water from the screen with a low-flow pump.
Sellwood et al. (2005)[17] proposed a modification of the approach by McCall et al. (2002)[20] to reduce profiling time and gain more information about subsurface stratigraphy. Instead of performing slug tests on the way down, slug tests were performed at different depths as the outer rod string was pulled up (Fig. 4). This way, the number of changes between the outer and inner rod strings was minimized (i.e., only one change needed at the bottom of the profile). Furthermore, an electrical conductivity (EC) probe was attached to the inner rod string so that EC data could be collected as the rod strings were advanced; the EC data could then be used for selecting the intervals for slug tests as the rod strings were retracted. This approach, called hydrostratigraphic profiling, enabled the collection of information on electrical and hydraulic conductivity to be obtained at a speed and resolution that had previously not been possible.
Borehole Flowmeter Profiling
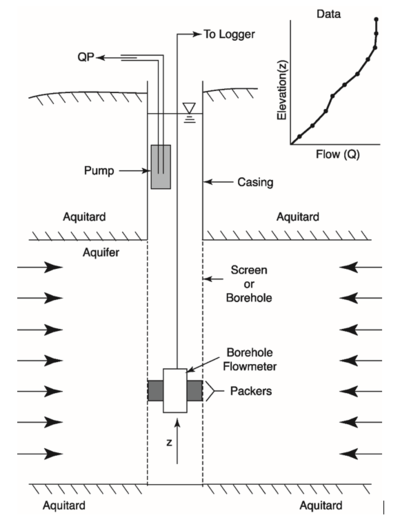
Borehole flowmeter profiling is one of the most efficient approaches for characterizing the vertical variations of K[21]. This approach involves pumping a well at a constant rate while measuring the vertical flow rate within the screened interval (Fig. 5). A flowmeter is initially positioned at the bottom of the screen. After the pump is turned on and the pumping rate stabilizes, the flowmeter is gradually moved up, often in an incremental fashion with short stops, although continuous profiling is also done. After the entire screened interval is measured, the profile of vertical flow rates versus depths can be used for K estimation. Typically, two profiles are performed, one prior to pumping and one during pumping. The profile obtained during pumping is corrected with the profile prior to pumping to remove the impacts of ambient flow in the well. Due to the difficulty of detecting small differences in flow rates, the K estimates from flowmeter profiling are subject to more noise in less permeable settings[22]. In addition, the results of flowmeter profiling are sensitive to in-well hydraulics, such as the impedance of flowmeter to vertical flow and disturbance by the pump intake when it is too close to the measurement interval[1].
Different types of flowmeters have been used for borehole profiling[23]. For example, electromagnetic flowmeters are often used in environmental site investigations due to their lower flow rate detection limit and lower head loss (high head loss across the flowmeter can cause flow bypass through the filter pack of the well). However, they may be more expensive than other options and have certain practical limitations as well[24]. Heat pulse flowmeters are also used for profiling in less-permeable settings.
The most common method of estimating K from borehole flowmeter profiles is based on the assumption that the lateral flow rate of an interval (zone between flow-rate measurements) is proportional to the K and thickness of that interval in a well fully screened in a perfectly layered aquifer,
where: | |
Ki | is the K of test interval i; |
Ka | is the average K for the entire screened interval; |
ΔQi | is the net lateral inflow across interval i, which can be calculated by subtracting the flow rate at the bottom of the interval from that at the top and taking ambient flow, if any, into account; |
Qt | is the total pumping rate; |
ΔBi | is the thickness of interval i; and |
Bt | is the total thickness of the aquifer. |
Ka can be obtained from pumping or slug tests at the same well, although it is generally recommended that slug tests be used, as the average K in the immediate vicinity of the well may differ from that determined from a pumping test in a laterally heterogeneous aquifer[1].
Figure 3 compares the results of borehole flowmeter profiling and multilevel slug tests at GEMS. Despite some local differences, the K estimates from borehole flowmeter profiling and multilevel slug tests are quite similar at that well.
DP Injection Logging
DP technology has shown great promise for characterization of K variations in shallow unconsolidated formations at the resolution, accuracy, and speed that are critically needed for practical investigations[25][26][27]. Over the last few decades, a series of DP methods and probes have been developed for obtaining information about vertical variations in K[1][2][28].
DP Injection Logging (DPIL) is one of the most powerful approaches for K characterization (in terms of resolution and speed of acquisition) and is also one of the most widely used techniques in environmental site investigations[2][29]. This approach consists of advancing a probe with a single screened port (Fig. 6A). Water is injected continuously through the screen while the probe is advanced and the pressure response to injection is monitored behind the screen or at the surface. The profile of the ratio of injection rate to injection pressure is closely related to vertical variations in K. However, factors other than the hydraulic conductivity can potentially affect the pressure response (e.g., injection line losses, probe advancement speed, formation alteration, and variations in specific storage), so DPIL ratios only provide relative information about K variations. Methods are needed for transforming DPIL ratios into actual K estimates; these methods typically involve correlations with nearby K data.
There are currently two variants of DPIL: discontinuous[28][30] and continuous[26][31][32] modes. In discontinuous DPIL mode, probe advancement is briefly halted at the desired depth and the injection rate is then varied in a step-wise fashion while injection rates and pressures are measured. In continuous DPIL mode, injection rate and pressure are measured as the probe is continuously advanced. Compared to continuous DPIL, discontinuous DPIL has a few advantages[2]:
- pore water pressure changes generated by probe advancement, which can be difficult to characterize, have little influence on the measured injection pressures;
- background hydrostatic pressures have no influence on the measured responses; and
- use of multiple injection rates at each depth allows a better assessment of the formation response to injection.
However, due to the need to halt advancement, discontinuous DPIL requires significantly more time than continuous DPIL, and, as a result, resolution below 10 - 20 cm is rarely possible. In common practice, continuous DPIL is generally preferred due to its speed (a 20-m profile requires about 2 hours) and resolution (one measurement per 1.5 cm vertical interval). A continuous DPIL probe, supplemented with an EC sensor, is commercially available from Geoprobe Systems under the tradename of the Hydraulic Profiling Tool (HPT; Fig. 6B).
The HPT is most effective in moderately permeable formations with a K range of 0.03 to 10 m/d, although the detection range can be improved by modifying equipment and operating procedures[2]. In standard HPT practice, the probe advancement rate is 2 cm/s and the continuous water injection rate is about 300 mL/min. In high K formations (e.g., K > 10 m/d), the injection pressure response to the standard injection rate is generally too small to be reliably measured. A larger injection rate can be used to increase the pressure signal. However, the line loss between the transducer and injection screen, which increases quadratically with the injection rate, may become significant and require additional step tests to remove its impact[2]. On the other hand, in low K formations (e.g., K < 0.03 m/d), the pressure increase from probe advancement and water injection may become so large that it will cause formation alterations and exceed the upper measurement limit of the transducer. A recent study has demonstrated that by reducing both probe advancement speed and flow injection rate, HPT can be applied to formations with K as low as 0.003 m/d[33].
Transforming DPIL profiles into K estimates is based on empirical relationships[26][28][32] [34]. Although a general relationship has been presented[34], site-specific calibrations are typically used to improve the reliability of K estimates. The site-specific calibrations can be performed by comparing the DPIL profiles to nearby K estimates obtained via other means[28][30] or by a modeling approach that directly combines the DPIL data with collocated hydraulic tests such as seen in Figure 6C, which shows a series of K profiles from continuous DPIL as calibrated by collocated hydraulic tests at an alluvial aquifer in Mississippi[32].
References
- ^ 1.0 1.1 1.2 1.3 1.4 1.5 1.6 1.7 Butler, J.J., 2005. Hydrogeological methods for estimation of spatial variations in hydraulic conductivity. In Hydrogeophysics (pp. 23-58). Springer, Dordrecht. doi: 10.1007/1-4020-3102-5_2
- ^ 2.0 2.1 2.2 2.3 2.4 2.5 Liu, G., Butler, J.J., Reboulet, E. and Knobbe, S., 2012. Hydraulic conductivity profiling with direct push methods. Grundwasser, 17(1), pp.19-29. doi: 10.1007/s00767-011-0182-9
- ^ 3.0 3.1 Freeze, R.A., Cherry, J.A. and Groundwater., A., 1979. Prentice-Hall. Inc., Englewood Cliffs, NJ ISBN 0-13-365312-9.
- ^ Darcy, H. (1856). Les Fontaines Publiques de la Ville de Dijon, Dalmont, Paris. doi: 10.1029/2001WR000727
- ^ 5.0 5.1 5.2 5.3 5.4 5.5 Butler Jr, J.J., 2009. Pumping tests for aquifer evaluation - Time for a change?. Groundwater, 47(5), pp.615-617. doi: 10.1111/j.1745-6584.2008.00488.x
- ^ Kabala, Z.J., 1993. The dipole flow test: A new single‐borehole test for aquifer characterization. Water Resources Research, 29(1), pp.99-107. doi: 10.1029/92WR01820
- ^ Zlotnik, V.A. and Zurbuchen, B.R., 1998. Dipole probe: Design and field applications of a single‐borehole device for measurements of vertical variations of hydraulic conductivity. Groundwater, 36(6), pp.884-893. doi: 10.1111/j.1745-6584.1998.tb02095.x
- ^ Datta‐Gupta, A., Yoon, S., Vasco, D.W. and Pope, G.A., 2002. Inverse modeling of partitioning interwell tracer tests: A streamline approach. Water Resources Research, 38(6), pp.15-1. doi: 10.1029/2001WR000597
- ^ Yeh, T.C.J. and Liu, S., 2000. Hydraulic tomography: Development of a new aquifer test method. Water Resources Research, 36(8), pp.2095-2105. Report.pdf
- ^ Bohling, G.C. and Butler Jr, J.J., 2010. Inherent limitations of hydraulic tomography. Groundwater, 48(6), pp.809-824. doi: 10.1111/j.1745-6584.2010.00757.x
- ^ Rasmussen, T.C., Haborak, K.G. and Young, M.H., 2003. Estimating aquifer hydraulic properties using sinusoidal pumping at the Savannah River site, South Carolina, USA. Hydrogeology Journal, 11(4), pp.466-482. doi: 10.1007/s10040-003-0255-7
- ^ Batu, V., 1998. Aquifer hydraulics: a comprehensive guide to hydrogeologic data analysis. John Wiley & Sons.
- ^ Kruseman, G.P., De Ridder, N.A. and Verweij, J.M., 1990. Analysis and evaluation of pumping test data – ILRI Pub. 47. The Netherlands: International institute for land reclamation and improvement
- ^ 14.0 14.1 14.2 Duffield, G.M., 2007. AQTESOLV for Windows Version 4.5 User's Guide. HydroSOLVE, Reston, VA.
- ^ 15.0 15.1 15.2 15.3 15.4 15.5 Butler Jr, J.J., 1997. The design, performance, and analysis of slug tests. Crc Press.
- ^ 16.0 16.1 Butler Jr, J.J., Garnett, E.J. and Healey, J.M., 2003. Analysis of slug tests in formations of high hydraulic conductivity. Groundwater, 41(5), pp.620-631. doi: 10.1111/j.1745-6584.2003.tb02400.x
- ^ 17.0 17.1 17.2 Sellwood, S.M., Healey, J.M., Birk, S. and Butler, J.J., 2005. Direct‐push hydrostratigraphic profiling: coupling electrical logging and slug tests. Ground water, 43(1), pp.19-29. doi: 10.1111/j.1745-6584.2005.tb02282.x
- ^ Hinsby, K., Bjerg, P.L., Andersen, L.J., Skov, B. and Clausen, E.V., 1992. A mini slug test method for determination of a local hydraulic conductivity of an unconfined sandy aquifer. Journal of Hydrology, 136(1-4), pp.87-106. doi: 10.1016/0022-1694(92)90006-H
- ^ Butler Jr, J.J., Healey, J.M., McCall, G.W., Garnett, E.J. and Loheide, S.P., 2002. Hydraulic tests with direct‐push equipment. Groundwater, 40(1), pp.25-36. doi: 10.1111/j.1745-6584.2002.tb02488.x
- ^ 20.0 20.1 20.2 McCall, W., J.J. Butler, Jr., J.M. Healey, A.A. Lanier, S.M. Sellwood, and E.J. Garnett, 2002. A dual-tube direct-push method for vertical profiling of hydraulic conductivity in unconsolidated formations, Environ. & Eng. Geoscience, 8(2), 75-84. doi: 10.2113/gseegeosci.8.2.75
- ^ 21.0 21.1 Molz, F.J., Morin, R.H., Hess, A.E., Melville, J.G. and Güven, O., 1989. The impeller meter for measuring aquifer permeability variations: evaluation and comparison with other tests. Water Resources Research, 25(7), pp.1677-1683. doi: 10.1029/WR025i007p01677
- ^ Bohling, G.C., Liu, G., Knobbe, S.J., Reboulet, E.C., Hyndman, D.W., Dietrich, P. and Butler, J.J., 2012. Geostatistical analysis of centimeter‐scale hydraulic conductivity variations at the MADE site. Water Resources Research, 48(2). doi: 10.1029/2011WR010791
- ^ Young, S.C. and Pearson, H.S., 1995. The electromagnetic borehole flowmeter: Description and application. Groundwater Monitoring & Remediation, 15(4), pp.138-147. doi: 10.1111/j.1745-6592.1995.tb00561.x
- ^ Bomana, G.K., Molz, F.J. and Boonec, K.D., 1997. Borehole flowmeter application in fluvial sediments: Methodology, results, and assessment. Groundwater, 35(3), pp.443-450. doi: 10.1111/j.1745-6584.1997.tb00104.x
- ^ Dietrich, P. and Leven, C., 2009. Direct push-technologies. In Groundwater geophysics (pp. 347-366). Springer, Berlin, Heidelberg.
- ^ 26.0 26.1 26.2 McCall, W., Nielsen, D.M., Farrington, S.P. and Christy, T.M., 2005. Use of direct-push technologies in environmental site characterization and ground-water monitoring. In Practical Handbook of Environmental Site Characterization and Ground-Water Monitoring, Second Edition (pp. 355-482). CRC Press. doi: 10.1201/9781420032246.ch6
- ^ Leven, C., Weiß, H., Vienken, T. and Dietrich, P., 2011. Direct-Push-Technologien–Effiziente Untersuchungsmethoden für die Untergrunderkundung. Grundwasser, 16(4), pp.221-234. doi: 10.1007/s00767-011-0175-8
- ^ 28.0 28.1 28.2 28.3 Dietrich, P., Butler Jr, J.J. and Faiß, K., 2008. A rapid method for hydraulic profiling in unconsolidated formations. Groundwater, 46(2), pp.323-328. doi: 10.1111/j.1745-6584.2007.00377.x
- ^ Maliva, R.G., 2016. Direct-push technology. In Aquifer Characterization Techniques (pp. 383-402). Springer, Cham. doi: 10.1007/978-3-319-32137-0_12
- ^ 30.0 30.1 Lessoff, Steven C., Uwe Schneidewind, Carsten Leven, Philipp Blum, Peter Dietrich, and Gedeon Dagan. "Spatial characterization of the hydraulic conductivity using direct‐push injection logging." Water Resources Research 46, no. 12 (2010). doi: 10.1029/2009WR008949
- ^ McCall, W., Christy, T.M., Christopherson, T. and Issacs, H., 2009. Application of direct push methods to investigate uranium distribution in an alluvial aquifer. Groundwater Monitoring & Remediation, 29(4), pp.65-76. doi: 10.1111/j.1745-6592.2009.01258.x
- ^ 32.0 32.1 32.2 Liu, G., Butler, J.J., Bohling, G.C., Reboulet, E., Knobbe, S. and Hyndman, D.W., 2009. A new method for high‐resolution characterization of hydraulic conductivity. Water Resources Research, 45(8). doi: 10.1029/2009WR008319
- ^ Liu, G., Borden, R.C. and Butler Jr, J.J., 2018. Simulation Assessment of Direct Push Injection Logging for High‐Resolution Aquifer Characterization. Groundwater. doi: 10.1111/gwat.12826
- ^ 34.0 34.1 McCall, W. and Christy, T.M., 2010. Development of a hydraulic conductivity estimate for the Hydraulic Profiling Tool (HPT). In The 2010 North American Environmental Field Conference & Exposition: Conference Program with Abstracts: Session VII.