Difference between revisions of "User:Jhurley/sandbox"
(→Wastewater Treatment Plants) |
(→Solid Waste Management Facilities) |
||
Line 74: | Line 74: | ||
==Solid Waste Management Facilities== | ==Solid Waste Management Facilities== | ||
− | Industrial, commercial, and consumer products containing PFAS that have been disposed in municipal solid waste (MSW) landfills or other legacy disposal areas since the 1950s are potential sources of PFAS release to the environment. Environmental and drinking water impacts from disposal of legacy PFAS-containing industrial and consumer wastes have been documented | + | Industrial, commercial, and consumer products containing PFAS that have been disposed in municipal solid waste (MSW) landfills or other legacy disposal areas since the 1950s are potential sources of PFAS release to the environment. Environmental and drinking water impacts from disposal of legacy PFAS-containing industrial and consumer wastes have been documented<ref name="Oliaei2010">Oliaei, F., Kriens, D. and Weber, R., 2010. Discovery and investigation of PFOS/PFCs contamination from a PFC manufacturing facility in Minnesota—environmental releases and exposure risks. Organohalogen Compd, 72, pp. 1338-1341.</ref><ref name="Shin2011"/><ref name="MDH2020">Minnesota Department of Health (MDH), 2020. Perfluoroalkyl Substances (PFAS) Sites in Minnesota. [https://www.health.state.mn.us/communities/environment/hazardous/topics/sites.html Website]</ref>. |
+ | |||
+ | Several studies have identified a wide variety of PFAS in MSW landfill leachates | ||
Revision as of 15:01, 29 January 2021
PFAS Sources
Perfluoroalkyl and Polyfluoroalkyl Substances (PFAS) have been used in coatings for textiles, paper products, and cookware; in some firefighting foams; and have a range of applications in the aerospace, photographic imaging, semiconductor, automotive, construction, electronics, and aviation industries[1][2][3]. Although PFAS and PFAS-containing products have been manufactured since the 1950s, PFAS were not widely documented in environmental samples until the early 2000s. Understanding PFAS manufacturing history, past and current uses, and waste management over the last six to seven decades is necessary for the identification of potential environmental sources of PFAS, possible release mechanisms, and associated pathway-receptor relationships.
Related Article(s):
Contributor(s): Dr. Sheau-Yun (Dora) Chiang and Dr. Alexandra Salter-Blanc
Key Resource(s):
Introduction
Perfluoroalkyl and Polyfluoroalkyl Substances (PFAS) are a complex family of more than 3,000 manmade fluorinated organic chemicals[4] although not all of these are currently in use or production. PFAS are produced using several different processes. Fluorosurfactants, which include perfluoroalkyl acids (PFAAs) (see PFAS article for nomenclature) and side-chain fluorinated polymers, have been manufactured using two major processes: electrochemical fluorination (ECF) and telomerization[2]. ECF was licensed by 3M in the 1940s[5] and used by 3M until 2001. ECF produces a mixture of even and odd numbered carbon chain lengths of approximately 70% linear and 30% branched substances[6]. Telomerization was developed in the 1970s[7], and yields mainly even numbered, straight carbon chain isomers[8][9]. PFAS manufacturers have provided PFAS to secondary manufacturers for production of a vast array of industrial and consumer products.
During manufacturing, PFAS may be released into the atmosphere then redeposited on land where they can also affect surface water and groundwater, or PFAS may be discharged without treatment to wastewater treatment plants or landfills, and eventually be released into the environment by treatment systems that are not designed to mitigate PFAS (see also PFAS Transport and Fate). Industrial discharges of PFAS were unregulated for many years, but that has begun to change. In January 2016, New York became the first state in the nation to regulate PFOA as a hazardous substance followed by the regulation of PFOS in April 2016. Consumer and industrial uses of PFAS-containing products can also end up releasing PFAS into landfills and into municipal wastewater, where it may accumulate undetected in biosolids which are typically treated by land application.
Industrial Sources
PFAS are used in many industrial and consumer applications, which may have released PFAS into the environment and impacted drinking water supplies in many areas of the United States[10]. Both in the United States (US) and abroad, primary manufacturing facilities produce PFAS and secondary manufacturing facilities use PFAS to produce goods. Environmental release mechanisms associated with these facilities include air emission and dispersion, spills, and disposal of manufacturing wastes and wastewater. Potential impacts to air, soil, sediment, surface water, stormwater, and groundwater are present not only at primary release points but potentially over the surrounding area[11]. Some of the potential primary and secondary sources of PFAS releases to the environment are listed here[1]:
- Textiles and leather: Factory or consumer applied coating to repel water, oil, and stains. Applications include protective clothing and outerwear, umbrellas, tents, sails, architectural materials, carpets, and upholstery[12][13][14][15][16][17][18][19][20][21][22][23][24][25][26][27].
- Paper products: Surface coatings to repel grease and moisture. Uses include non-food paper packaging (for example, cardboard, carbonless forms, masking papers) and food-contact materials (for example, pizza boxes, fast food wrappers, microwave popcorn bags, baking papers, pet food bags)[12][8][13][15][18][22][23][26][28]
- Metal Plating & Etching: Corrosion prevention, mechanical wear reduction, aesthetic enhancement, surfactant, wetting agent/fume suppressant for chrome, copper, nickel and tin electroplating, and post-plating cleaner[29][30][8][16][31][23][32][2][33]
- Industrial Surfactants, Resins, Molds, Plastics: Manufacture of plastics and fluoropolymers, rubber, and compression mold release coatings; plumbing fluxing agents; fluoroplastic coatings, composite resins, and flame retardant for polycarbonate[8][36][15][37][16][38][34][22][24][26][39]
- Photolithography, Semiconductor Industry: Photoresists, top anti-reflective coatings, bottom anti-reflective coatings, and etchants, with other uses including surfactants, wetting agents, and photo-acid generation[40][41][14][34][23][24]
Class B Firefighting Foams
Aqueous film forming foam (AFFF) and other fluorinated Class B firefighting foams are another important source of PFAS to the environment, especially in military and aviation settings. Class B firefighting foams have been used since the 1960s to extinguish flammable liquid hydrocarbon fires and for vapor suppression. These foams contain complex and variable mixtures of PFAS that act as surfactants. Fluorinated surfactants are both hydrophobic and oleophobic (oil-repelling), as well as thermally stable, chemically stable, and highly surface active[42]. These properties make them uniquely suited to fighting hydrocarbon fuel fires. Use of fluorinated Class B foams is prevalent and is a major source of PFAS to the environment. Release to the environment typically occurs during firefighting operations, firefighter training, apparatus testing, or leakage during storage. Research into fluorine-free alternatives is underway and Congressional pressure is leading towards banning fluorinated Class B firefighting foams in the United States.
When discussing the relationship between firefighting foams and sources of PFAS to the environment, the emphasis is typically on AFFF; however, many different types of Class B firefighting foams exist. These may or may not be fluorinated (contain PFAS). Class B foams are used to extinguish Class B fires, that is, those involving flammable liquids. Fluorinated Class B foams spread across the surface of the flammable liquid forming a thin film and extinguish fires by (1) excluding air from the flammable vapors, (2) suppressing vapor release, (3) physically separating the flames from the fuel source, and (4) cooling the fuel surface and surrounding metal surfaces[43]. From a PFAS perspective, Class B firefighting foams can be divided into two broad categories: fluorinated foams (that contain PFAS) and fluorine-free foams (that do not contain PFAS)[1]. This distinction and examples of each type are shown in Figure 1.
AFFF was developed by the US Navy in the 1960s and in 1969, the US Department of Defense (DoD) issued military specification MIL-F-24385 listing firefighting performance requirements for all AFFF used within the US DoD[1][44][45]. These performance standards are often referred to as “Mil-Spec.” Products that meet the Mil-Spec have been added to the US DoD Qualified Product Listing (QPL). In 2006 the US Federal Aviation Administration (FAA) also began requiring that 14-CFR-139-certified commercial airports purchase Mil-Spec compliant AFFF only. Because the US DoD and FAA have been the primary purchasers of AFFF, development of AFFF product mixtures has historically been performance-driven (to comply with the Mil-Spec) rather than formula-driven (the specific PFAS mixtures utilized have varied over time and by manufacturer). Multiple manufacturers in the US and throughout the world produce or have produced AFFF concentrate[1]. AFFF concentrate is or has been available in 1%, 3%, or 6% formulations, where the percentage designates the recommended percentage of concentrate to be mixed into water during application.
The specific mixtures of PFAS found in AFFF have varied by manufacturer and over time due to differences in production processes and voluntary formula changes. AFFF formulations can generally be grouped into three categories[1]:
- Legacy Perfluorooctane Sulfonate (PFOS) AFFF This type of AFFF was manufactured exclusively by 3M under the brand name “Lightwater” from the late 1960s until 2002 using the ECF production process. They contain PFOS and perflouroalkane sulfonates (PFSAs) such as perfluorohexane sulfonate (PFHxS)[1][46]. Legacy PFOS AFFF produced by ECF were voluntarily phased out in 2002, however, use of stockpiled product was permitted after that date[1].
- Legacy fluorotelomer AFFF This group consists of AFFF manufactured and sold in the U.S. from the 1970s until 2016 and includes all brands that were produced using a process known as fluorotelomerization (FT). The FT manufacturing process produces polyfluorinated substances that can degrade in the environment to perfluoroalkyl substances (specifically PFAAs) including Perfluorooctanoic Acid (PFOA). Polyfluoroalkyl substances that degrade to create terminal PFAAs are referred to as “precursors” [1].
- Modern fluorotelomer AFFF This group consists of AFFF developed in response to the USEPA 2010-2015 voluntary PFOA Stewardship Program[47], which asked companies to commit to first reducing and then eliminating the following: PFOA, precursors that can break down to PFOA, and related chemicals from facility emissions and products. In response, manufacturers began producing only short-chain fluorosurfactants targeting fluorotelomer PFAS with 6 carbons per chain (C6), rather than the traditional long-chain fluorosurfactants (8 or more carbons per chain). These short-chain PFAS do not breakdown in the environment to PFOS or PFOA[1]. Their toxicity in comparison to long-chain fluorosurfactants is a topic of current research.
In the US, AFFF users including the US DoD (predominantly the Navy and Air Force), civilian airports, oil refineries, other petrochemical industries, and municipal fire departments[48]. AFFF is used, for example, in fire fighting vehicles, in fixed fire suppression systems (including sprinklers and fixed spray systems in or at aircraft hangars, flammable liquid storage areas, engine hush houses, and fuel farms), and onboard military and commercial ships. Fluorinated Class B foams may be introduced to the environment through the following practices[1]:
- low volume releases of foam concentrate during storage, transfer or operational requirements that mandate periodic equipment calibration
- moderate volume discharge of foam solution for apparatus testing and episodic discharge of AFFF-containing fire suppression systems within large aircraft hangars and buildings
- occasional, high-volume, broadcast discharge of foam solution for firefighting and fire suppression/prevention for emergency response
- periodic, high volume, broadcast discharge for fire training
- accidental leaks from foam distribution piping between storage and pumping locations, and from storage tanks and railcars
The DoD is currently replacing legacy, long-chain AFFF with modern, short-chain fluorotelomer AFFF and disposing of the legacy foams through incineration. While the PFAS included in modern fluorotelomer AFFF formulations are currently understood to be less toxic and less bioaccumulative than those used in legacy formulations, they are also environmentally persistent and can degrade to produce other PFAS that may pose environmental concerns[1]. While fluorine free alternatives exist, they do not meet the current Mil-Spec[45] which requires that fluorine-based compounds be used. The US DoD is working to revise the Mil-Spec to allow fluorine-free foams, and several states have passed laws prohibiting the use of fluorinated Class B foams for training and prohibiting future manufacture, sale or distribution of fluorinated foams, with limited exceptions[49] (e.g., WA Rev Code § 70.75A.005 (2019); VA § 9.1-207.1 (2019)). Additionally, a bill passed in the US Congress in 2018 directs the FAA to allow fluorine-free foams for use at commercial airports[50]. Research into the development of Mil-Spec compliant fluorine-free foams that will be compatible with existing AFFF and supporting equipment is ongoing and includes the following:
- Novel Fluorine-Free Replacement for Aqueous Film Forming Foam (Lead investigator: Dr. Joseph Tsang, Naval Air Warfare Center Weapons Divisions) SERDP/ESTCP Project WP-2737
- Fluorine-Free Aqueous Film Forming Foam (Lead investigator: Dr. John Payne, National Foam) SERDP/ESTCP Project WP-2738
- Fluorine-Free Foams with Oleophobic Surfactants and Additives for Effective Pool fire Suppression (Lead investigator: Dr. Ramagopal Ananth, U.S. Naval Research Laboratory) SERDP/ESTCP Project WP-2739
Wastewater Treatment Plants
Consumer and/or industrial uses of PFAS-containing materials results in the discharge of PFAS to industrial and municipal wastewater treatment plants (WWTPs). Conventional WWTP treatment processes remove less than 5% of PFAAs[21][51][52]. WWTPs, particularly those that receive industrial wastewater, are possible sources of PFAS release[53][54][55].
Evaluation of full-scale WWTPs has indicated that conventional primary (sedimentation and clarification) and secondary (aerobic biodegradation of organic matter) treatment processes can result in changes in PFAS concentrations and classes. For example, higher concentrations of PFAAs have been observed in effluent than in influent, presumably due to transformation of precursor PFAS[51]. Some data has indicated that the terminal PFAS compounds PFOS and PFOA were among the most frequently detected PFAS in wastewater[56]. A state-wide study in Michigan indicated that PFAS were detected in all of the samples from 42 WWTPs, including influent, effluent, and biosolids/sludge samples, and that the short-chain PFAS were more frequently detected in the liquid process flow (influent and effluent), while long-chain PFAS were more common in biosolids[57].
Multiple studies have found PFAS in municipal sewage sludge[58][57]. The US EPA states that more than half of the sludge produced in the United States is applied to agricultural land as biosolids, therefore there are concerns that biosolids applications may become a potential source of PFAS to the environment[59]. Application of biosolids as a soil amendment can potentially result in transfer of PFAS to soil, surface water and groundwater and can possibly allow PFAS to enter the food chain[60][61][62][63][64]. Limited studies have shown that PFAS concentrations can be elevated in surface and groundwater in the vicinity of agricultural fields that received PFAS contaminated biosolids for an extended period[65]. The most abundant PFAS found in biosolids are the long-chain PFAS[56][57]. Based on the persistence and stability of long-chain PFAS and their interaction with biosolids, research is ongoing to determine PFAS leachability from biosolids and their bioavailability for uptake by plants, soil organisms, and the consumers of potentially PFAS-impacted plants and soil organisms.
Solid Waste Management Facilities
Industrial, commercial, and consumer products containing PFAS that have been disposed in municipal solid waste (MSW) landfills or other legacy disposal areas since the 1950s are potential sources of PFAS release to the environment. Environmental and drinking water impacts from disposal of legacy PFAS-containing industrial and consumer wastes have been documented[66][11][67].
Several studies have identified a wide variety of PFAS in MSW landfill leachates
One other implication of matrix diffusion is that plume migration is attenuated by the loss of contaminants into low permeability zones, leading to slower plume migration compared to a case where no matrix diffusion occurs. This phenomena was observed as far back as 1985 when Sudicky et al. observed that “A second consequence of the solute-storage effect offered by transverse diffusion into low-permeability layers is a rate of migration of the frontal portion of a contaminant in the permeable layers that is less than the groundwater velocity.”[69] In cases where there is an attenuating source, matrix diffusion can also reduce the peak concentrations observed in downgradient monitoring wells. The attenuation caused by matrix diffusion may be particularly important for implementing Monitored Natural Attenuation (MNA) for contaminants that do not completely degrade, such as heavy metals and Perfluoroalkyl and Polyfluoroalkyl Substances (PFAS).
SERPD/ESTCP Research
The SERDP/ESTCP programs have funded several projects focusing on how matrix diffusion can impede progress towards reaching site closure, including: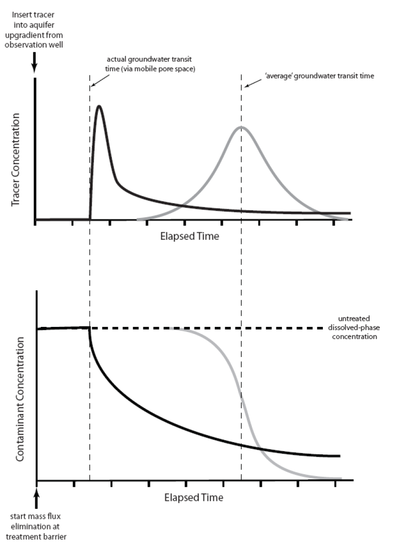
Transport Modeling
Several different modeling approaches have been developed to simulate the diffusive transport of dissolved solutes into and out of lower K zones[75][76]. The Matrix Diffusion Toolkit[71] is a Microsoft Excel based tool for simulating forward and back diffusion using two different analytical models[77][78]. Numerical models including MODFLOW/MT3DMS[79] have been shown to be effective in simulating back diffusion processes and can accurately predict concentration changes over 3 orders-of-magnitude in heterogeneous sand tank experiments[80]. However, numerical models require a fine vertical discretization with short time steps to accurately simulate back diffusion, greatly increasing computation times[81]. These issues can be addressed by incorporating a local 1-D model domain within a general 3D numerical model[82].
The REMChlor - MD toolkit is capable of simulating matrix diffusion in groundwater contaminant plumes by using a semi-analytical method for estimating mass transfer between high and low permeability zones that provides computationally accurate predictions, with much shorter run times than traditional fine grid numerical models[73].
Impacts on Breakthrough Curves
The impacts of matrix diffusion on the initial breakthrough of the solute plume and on later cleanup are illustrated in Figure 3[74]. Using a traditional advection-dispersion model, the breakthrough curve for a pulse tracer injection appears as a bell-shaped (Gaussian) curve (gray line on the right side of the upper graph) where the peak arrival time corresponds to the average groundwater velocity. Using an advection-diffusion approach, the breakthrough curve for a pulse injection is asymmetric (solid black line) with the peak tracer concentration arriving earlier than would be expected based on the average groundwater velocity, but with a long extended tail to the flushout curve.
The lower graph shows the predicted cleanup concentration profiles following complete elimination of a source area. The advection-dispersion model (gray line) predicts a clean-water front arriving at a time corresponding to the average groundwater velocity. The advection-diffusion model (black line) predicts that concentrations will start to decline more rapidly than expected (based on the average groundwater velocity) as clean water rapidly migrates through the highest-permeability strata. However, low but significant contaminant concentrations linger much longer (tailing) due to diffusive contaminant mass exchange between zones of high and low permeability. A similar response to source remediation is seen in models such as the sand tank experiment shown in Figure 2, and also in field observations of plume contaminant concentrations in heterogeneous aquifers.
References
- ^ 1.00 1.01 1.02 1.03 1.04 1.05 1.06 1.07 1.08 1.09 1.10 1.11 1.12 Interstate Technology and Regulatory Council (ITRC), 2020. Technical/Regulatory Guidance: Per- and Polyfluoroalkyl Substances (PFAS), PFAS-1. ITRC, PFAS Team, Washington DC. Website: https://pfas-1.itrcweb.org/ Free Download from ITRC. Report.pdf
- ^ 2.0 2.1 2.2 Swedish Chemicals Agency (KEMI), 2015. Occurrence and use of highly fluorinated substances and alternatives, Report 7/15. ISSN 0284-1185. Article number 361 164. Report.pdf
- ^ US Environmental Protection Agency (USEPA), 2021. Basic Information on PFAS. Website
- ^ Wang, Z., DeWitt, J.C., Higgins, C.P., and Cousins, I.T., 2017. A Never-Ending Story of Per- and Poly-Fluoroalkyl Substances (PFASs)? Environmental Science and Technology, 51(5), pp. 2508-2518. DOI: 10.1021/acs.est.6b04806 Open access article.
- ^ Banks, R.E., Smart, B.E. and Tatlow, J.C. eds., 1994. Organofluorine Chemistry: Principles and Commercial Applications. Springer Science and Business Media, New York, N. Y. DOI: 10.1007/978-1-4899-1202-2
- ^ Concawe (Conservation of Clean Air and Water in Europe), 2016. Environmental fate and effects of poly- and perfluoroalkyl substances (PFAS). Report No. 8/16. Brussels, Belgium. Report.pdf
- ^ Benskin, J.P., Ahrens, L., Muir, D.C., Scott, B.F., Spencer, C., Rosenberg, B., Tomy, G., Kylin, H., Lohmann, R. and Martin, J.W., 2012. Manufacturing Origin of Perfluorooctanoate (PFOA) in Atlantic and Canadian Arctic Seawater. Environmental Science and Technology, 46(2), pp. 677-685. DOI: 10.1021/es202958p
- ^ 8.0 8.1 8.2 8.3 8.4 Kissa, E., 2001. Fluorinated Surfactants and Repellents, Second Edition. Surfactant Science Series, Vol. 97. Marcel Dekker, Inc., CRC Press, New York. 640 pages. ISBN: 9780824704728
- ^ Parsons, J.R., Sáez, M., Dolfing, J. and De Voogt, P., 2008. Biodegradation of Perfluorinated Compounds. Reviews of Environmental Contamination and Toxicology, 196, pp. 53-71. Springer, New York, NY. DOI: 10.1007/978-0-387-78444-1_2 Free download from: ResearchGate
- ^ Environmental Working Group (EWG) and Northeastern University Social Science Environmental Health Research Institute, 2017. Mapping A Contamination Crisis. Website
- ^ 11.0 11.1 Shin, H.M., Vieira, V.M., Ryan, P.B., Detwiler, R., Sanders, B., Steenland, K., and Bartell, S.M., 2011. Environmental Fate and Transport Modeling for Perfluorooctanoic Acid Emitted from the Washington Works Facility in West Virginia. Environmental Science and Technology, 45(4), pp. 1435-1442. DOI: 10.1021/es102769t
- ^ 12.0 12.1 Rao, N.S., and Baker, B.E., 1994. Textile Finishes and Fluorosurfactants. In: Organofluorine Chemistry, Banks, R.E., Smart, B.E., and Tatlow, J.C., Eds. Springer, New York. DOI: 10.1007/978-1-4899-1202-2_15
- ^ 13.0 13.1 Hekster, F.M., Laane, R.W. and De Voogt, P., 2003. Environmental and Toxicity Effects of Perfluoroalkylated Substances. Reviews of Environmental Contamination and Toxicology, 179, pp. 99-121. Springer, New York, NY. DOI: 10.1007/0-387-21731-2_4
- ^ 14.0 14.1 Brooke, D., Footitt, A., and Nwaogu, T.A., 2004. Environmental Risk Evaluation Report: Perfluorooctanesulphonate (PFOS). Environment Agency (UK), Science Group. Free download from: The Stockholm Convention Report.pdf
- ^ 15.0 15.1 15.2 Poulsen, P.B., Jensen, A.A., and Wallström, E., 2005. More environmentally friendly alternatives to PFOS-compounds and PFOA. Danish Environmental Protection Agency, Environmental Project 1013. Report.pdf
- ^ 16.0 16.1 16.2 Prevedouros, K., Cousins, I.T., Buck, R.C. and Korzeniowski, S.H., 2006. Sources, Fate and Transport of Perfluorocarboxylates. Environmental Science and Technology, 40(1), pp. 32-44. DOI: 10.1021/es0512475 Free download from: Academia.edu
- ^ Walters, A., and Santillo, D., 2006. Technical Note 06/2006: Uses of Perfluorinated Substances. Greenpeace Research Laboratories. Website Report.pdf
- ^ 18.0 18.1 Trudel, D., Horowitz, L., Wormuth, M., Scheringer, M., Cousins, I.T. and Hungerbühler, K., 2008. Estimating Consumer Exposure to PFOS and PFOA. Risk Analysis: An International Journal, 28(2), pp. 251-269. DOI: 10.1111/j.1539-6924.2008.01017.x
- ^ Guo, Z., Liu, X., Krebs, K.A. and Roache, N.F., 2009. Perfluorocarboxylic Acid Content in 116 Articles of Commerce, EPA/600/R-09/033. National Risk Management Research Laboratory, US Environmental Protection Agency, Washington, DC. Available from: US EPA. Report.pdf
- ^ US Environmental Protection Agency (USEPA), 2009. Long-Chain Perfluorinated Chemicals (PFCs), Action Plan. Website Report.pdf
- ^ 21.0 21.1 Ahrens, L., 2011. Polyfluoroalkyl compounds in the aquatic environment: a review of their occurrence and fate. Journal of Environmental Monitoring, 13(1), pp.20-31. DOI: 10.1039/C0EM00373E. Free download available from: ResearchGate
- ^ 22.0 22.1 22.2 Buck, R.C., Franklin, J., Berger, U., Conder, J.M., Cousins, I.T., De Voogt, P., Jensen, A.A., Kannan, K., Mabury, S.A. and van Leeuwen, S.P., 2011. Perfluoroalkyl and Polyfluoroalkyl Substances in the Environment: Terminology, Classification, and Origins. Integrated Environmental Assessment and Management, 7(4), pp. 513-541. DOI: 10.1002/ieam.258 Open access article.
- ^ 23.0 23.1 23.2 23.3 United Nations Environmental Programme (UNEP), 2011. Report of the persistent organic pollutants review committee on the work of its sixth meeting, Addendum, Guidance on alternatives to perfluorooctane sulfonic acid and its derivatives, UNEP/POPS/POPRC.6/13/Add.3/Rev.1 Website Report.pdf
- ^ 24.0 24.1 24.2 Herzke, D., Olsson, E. and Posner, S., 2012. Perfluoroalkyl and polyfluoroalkyl substances (PFASs) in consumer products in Norway – A pilot study. Chemosphere, 88(8), pp. 980-987. DOI: 10.1016/j.chemosphere.2012.03.035
- ^ Patagonia, Inc., 2016. An Update on Our DWR Problem. Website Report.pdf
- ^ 26.0 26.1 26.2 Kotthoff, M., Müller, J., Jürling, H., Schlummer, M., and Fiedler, D., 2015. Perfluoroalkyl and polyfluoroalkyl substances in consumer products. Environmental Science and Pollution Research, 22(19), pp. 14546-14559. DOI: 10.1007/s11356-015-4202-7 Open access article.
- ^ Agency for Toxic Substances and Disease Registry (ATSDR), 2018. Toxicological Profile for Perfluoroalkyls, Draft for Public Comment. US Department of Health and Human Services. Free download from: ATSDR Report.pdf
- ^ Schaider, L.A., Balan, S.A., Blum, A., Andrews, D.Q., Strynar, M.J., Dickinson, M.E., Lunderberg, D.M., Lang, J.R., and Peaslee, G.F., 2017. Fluorinated Compounds in US Fast Food Packaging. Environmental Science and Technology Letters, 4(3), pp. 105-111. DOI: 10.1021/acs.estlett.6b00435 Open access article.
- ^ US Environmental Protection Agency (USEPA), 1996. Emission Factor Documentation for AP-42, Section 12.20. Office of Air Quality Planning and Standards, Emission Factor and Inventory Group, Research Triangle Park, NC. Report.pdf
- ^ Riordan, B.J., Karamchandanl, R.T., Zitko, L.J., and Cushnie Jr., G.C., 1998. Capsule Report: Hard Chrome Fume Suppressants and Control Technologies. Center for Environmental Research Information, National Risk Management Research Laboratory, Office of Research and Development. EPA/625/R-98/002 Website Report.pdf
- ^ US Environmental Protection Agency (USEPA), 2009. PFOS Chromium Electroplater Study. US EPA – Region 5, Chicago, IL. Report.pdf
- ^ Occupational Safety and Health Agency (OSHA), 2013. Fact Sheet: Controlling Hexavalent Chromium Exposures during Electroplating. United States Department of Labor. Report.pdf
- ^ Danish Environmental Protection Agency, 2015. Alternatives to perfluoroalkyl and polyfluoroalkyl substances (PFAS) in textiles. Report.pdf
- ^ 34.0 34.1 34.2 van der Putte, I., Murin, M., van Velthoven, M., and Affourtit, F., 2010. Analysis of the risks arising from the industrial use of Perfluorooctanoic acid (PFOA) and Ammonium Perfluorooctanoate (APFO) and from their use in consumer articles. Evaluation of the risk reduction measures for potential restrictions on the manufacture, placing on the market and use of PFOA and APFO. RPS Advies, Delft, The Netherlands for European Commission Enterprise and Industry Directorate-General. Website Report.pdf
- ^ Association of State and Territorial Solid Waste Management Officials (ASTSWMO), 2015. Perfluorinated Chemicals (PFCs): Perfluorooctanoic Acid (PFOA) and Perfluorooctane Sulfonate (PFOS) Information Paper. Remediation and Reuse Focus Group, Federal Facilities Research Center, Washington, D.C. Free download from: US EPA Report.pdf
- ^ Renner, R., 2001. Growing Concern Over Perfluorinated Chemicals. Environmental Science and Technology, 35(7), pp. 154A-160A. DOI: 10.1021/es012317k Open access article.
- ^ Fricke, M. and Lahl, U., 2005. Risk Evaluation of Perfluorinated Surfactants as Contribution to the current Debate on the EU Commission’s REACH Document. Umweltwissenschaften und Schadstoff-Forschung (UWSF), 17(1), pp. 36-49. DOI: 10.1007/BF03038694
- ^ Skutlarek, D., Exner, M. and Färber, H., 2006. Perfluorinated Surfactants in Surface and Drinking Waters. Environmental Science and Pollution Research International, 13(5), pp. 299-307. DOI: 10.1065/espr2006.07.326 Free download from: ResearchGate
- ^ Chemours, 2010. The History of Teflon Fluoropolymers. Website
- ^ Choi, D.G., Jeong, J.H., Sim, Y.S., Lee, E.S., Kim, W.S. and Bae, B.S., 2005. Fluorinated Organic− Inorganic Hybrid Mold as a New Stamp for Nanoimprint and Soft Lithography. Langmuir, 21(21), pp. 9390-9392. DOI: 10.1021/la0513205
- ^ Rolland, J.P., Van Dam, R.M., Schorzman, D.A., Quake, S.R., and DeSimone, J.M., 2004. Solvent-Resistant Photocurable “Liquid Teflon” for Microfluidic Device Fabrication. Journal of the American Chemical Society, 126(8), pp. 2322-2323. DOI: 10.1021/ja031657y
- ^ Moody, C.A. and Field, J.A., 1999. Determination of Perfluorocarboxylates in Groundwater Impacted by Fire-Fighting Activity. Environmental Science and Technology, 33(16), pp. 2800-2806. DOI: 10.1021/es981355+
- ^ National Foam, no date. A Firefighter’s Guide to Foam. Website Report.pdf
- ^ Backe, W.J., Day, T.C. and Field, J.A., 2013. Zwitterionic, Cationic, and Anionic Fluorinated Chemicals in Aqueous Film Forming Foam Formulations and Groundwater from US Military Bases by Nonaqueous Large-Volume Injection HPLC-MS/MS. Environmental Science and Technology, 47(10), pp. 5226-5234. DOI: 10.1021/es3034999
- ^ US Environmental Protection Agency (USEPA), 2018. Fact Sheet: 2010/2015 PFOA Stewardship Program. Website
- ^ Darwin, Robert L. 2011. Estimated Inventory of PFOS-based Aqueous Film Forming Foam (AFFF). Fire Fighting Foam Coalition, Inc., Arlington, VA. Report.pdf
- ^ Denton, Charles, 2019. Expert Focus: US states outpace EPA on PFAS firefighting foam laws. Chemical Watch. Website
- ^ FAA Reauthorization Act of 2018. US Public Law No: 115-254 (10/05/2018). Website Report.pdf
- ^ 51.0 51.1 Schultz, M.M., Higgins, C.P., Huset, C.A., Luthy, R.G., Barofsky, D.F., and Field, J.A., 2006. Fluorochemical Mass Flows in a Municipal Wastewater Treatment Facility. Environmental Science and Technology, 40(23), pp. 7350-7357. DOI: 10.1021/es061025m Author Manuscript
- ^ Michigan Waste and Recycling Association (MWRA), 2019. Statewide Study on Landfill Leachate PFOA and PFOS Impact on Water Resource Recovery Facility Influent, Second Revision. Report.pdf
- ^ Bossi, R., Strand, J., Sortkjær, O. and Larsen, M.M., 2008. Perfluoroalkyl compounds in Danish wastewater treatment plants and aquatic environments. Environment International, 34(4), pp. 443-450. DOI: 10.1016/j.envint.2007.10.002 Free download from: Academia.edu
- ^ Lin, A.Y.C., Panchangam, S.C., Tsai, Y.T., and Yu, T.H., 2014. Occurrence of perfluorinated compounds in the aquatic environment as found in science park effluent, river water, rainwater, sediments, and biotissues. Environmental Monitoring and Assessment, 186(5), pp. 3265-3275. DOI: 10.1007/s10661-014-3617-9
- ^ Ahrens, L., Felizeter, S., Sturm, R., Xie, Z. and Ebinghaus, R., 2009. Polyfluorinated compounds in waste water treatment plant effluents and surface waters along the River Elbe, Germany. Marine Pollution Bulletin, 58(9), pp.1326-1333. DOI: 10.1016/j.marpolbul.2009.04.028 Author’s manuscript
- ^ 56.0 56.1 Hamid, H. and Li, L., 2016. Role of wastewater treatment plant in environmental cycling of poly- and perfluoroalkyl substances. Ecocycles, 2(2), pp. 43-53. DOI: 10.19040/ecocycles.v2i2.62 Open access article.
- ^ 57.0 57.1 57.2 Michigan Department of Environment, Great Lakes and Energy (EGLE), 2020. Summary Report: Initiatives to Evaluate the Presence of PFAS in Municipal Wastewater and Associated Residuals (Sludge/Biosolids) in Michigan. Report.pdf Website
- ^ Higgins, C.P., Field, J.A., Criddle, C.S., and Luthy, R.G., 2005. Quantitative Determination of Perfluorochemicals in Sediments and Domestic Sludge. Environmental Science and Technology, 39 (11), pp. 3946 – 3956. DOI: 10.1021/es048245p
- ^ US Environmental Protection Agency (USEPA), 2020. Research on Per- and Polyfluoroalkyl Substances (PFAS). Website
- ^ Sepulvado, J.G., Blaine, A.C., Hundal, L.S. and Higgins, C.P., 2011. Occurrence and Fate of Perfluorochemicals in Soil Following the Land Application of Municipal Biosolids. Environmental Science and Technology, 45(19), pp. 8106-8112. DOI: 10.1021/es103903d
- ^ Lindstrom, A.B., Strynar, M.J., Delinsky, A.D., Nakayama, S.F., McMillan, L., Libelo, E.L., Neill, M. and Thomas, L., 2011. Application of WWTP Biosolids and Resulting Perfluorinated Compound Contamination of Surface and Well Water in Decatur, Alabama, USA. Environmental Science and Technology, 45(19), pp. 8015-8021. DOI: 10.1021/es1039425
- ^ Blaine, A.C., Rich, C.D., Hundal, L.S., Lau, C., Mills, M.A., Harris, K.M. and Higgins, C.P., 2013. Uptake of Perfluoroalkyl Acids into Edible Crops via Land Applied Biosolids: Field and Greenhouse Studies. Environmental Science and Technology, 47(24), pp.14062-14069. DOI: 10.1021/es403094q Free download from: US EPA
- ^ Blaine, A.C., Rich, C.D., Sedlacko, E.M., Hundal, L.S., Kumar, K., Lau, C., Mills, M.A., Harris, K.M. and Higgins, C.P., 2014. Perfluoroalkyl Acid Distribution in Various Plant Compartments of Edible Crops Grown in Biosolids-Amended Soils. Environmental Science and Technology, 48(14), pp. 7858-7865. DOI: 10.1021/es500016s Free download from: ResearchGate
- ^ Washington, J.W., Yoo, H., Ellington, J.J., Jenkins, T.M., and Libelo, E.L., 2010. Concentrations, Distribution, and Persistence of Perfluoroalkylates in Sludge-Applied Soils near Decatur, Alabama, USA. Environmental Science and Technology, 44(22), pp. 8390-8396. DOI: 10.1021/es1003846 Free download from: ResearchGate
- ^ Oliaei, F., Kriens, D. and Weber, R., 2010. Discovery and investigation of PFOS/PFCs contamination from a PFC manufacturing facility in Minnesota—environmental releases and exposure risks. Organohalogen Compd, 72, pp. 1338-1341.
- ^ Minnesota Department of Health (MDH), 2020. Perfluoroalkyl Substances (PFAS) Sites in Minnesota. Website
- ^ Sale, T.C., Illangasekare, T.H., Zimbron, J., Rodriguez, D., Wilking, B., and Marinelli, F., 2007. AFCEE Source Zone Initiative. Air Force Center for Environmental Excellence, Brooks City-Base, San Antonio, TX. Report.pdf
- ^ Sudicky, E.A., Gillham, R.W., and Frind, E.O., 1985. Experimental Investigation of Solute Transport in Stratified Porous Media: 1. The Nonreactive Case. Water Resources Research, 21(7), pp. 1035-1041. DOI: 10.1029/WR021i007p01035
- ^ Cite error: Invalid
<ref>
tag; no text was provided for refs namedSale2013
- ^ 71.0 71.1 Farhat, S.K., Newell, C.J., Seyedabbasi, M.A., McDade, J.M., Mahler, N.T., Sale, T.C., Dandy, D.S. and Wahlberg, J.J., 2012. Matrix Diffusion Toolkit. Environmental Security Technology Certification Program (ESTCP) Project ER-201126. User’s Manual.pdf Website: ER-201126
- ^ Sale, T. and Newell, C., 2011. A Guide for Selecting Remedies for Subsurface Releases of Chlorinated Solvents. Environmental Security Technology Certification Program (ESTCP) Project ER-200530. Report.pdf Website: ER-200530
- ^ 73.0 73.1 Farhat, S. K., Newell, C. J., Falta, R. W., and Lynch, K., 2018. A Practical Approach for Modeling Matrix Diffusion Effects in REMChlor. Environmental Security Technology Certification Program (ESTCP) Project ER-201426. User’s Manual.pdf Website: ER-201426
- ^ 74.0 74.1 Interstate Technology and Regulatory Council (ITRC), 2011. Integrated DNAPL Site Strategy (IDSS-1), Integrated DNAPL Site Strategy Team, ITRC, Washington, DC. Report.pdf Free download from: ITRC
- ^ Falta, R.W., and Wang, W., 2017. A semi-analytical method for simulating matrix diffusion in numerical transport models. Journal of Contaminant Hydrology, 197, pp. 39-49. DOI: 10.1016/j.jconhyd.2016.12.007
- ^ Muskus, N. and Falta, R.W., 2018. Semi-analytical method for matrix diffusion in heterogeneous and fractured systems with parent-daughter reactions. Journal of Contaminant Hydrology, 218, pp. 94-109. DOI: 10.1016/j.jconhyd.2018.10.002
- ^ Parker, B.L., Gillham, R.W., and Cherry, J.A., 1994. Diffusive Disappearance of Immiscible Phase Organic Liquids in Fractured Geologic Media. Groundwater, 32(5), pp. 805-820. DOI: 10.1111/j.1745-6584.1994.tb00922.x
- ^ Sale, T.C., Zimbron, J.A., and Dandy, D.S., 2008. Effects of reduced contaminant loading on downgradient water quality in an idealized two-layer granular porous media. Journal of Contaminant Hydrology, 102(1), pp. 72-85. DOI: 10.1016/j.jconhyd.2008.08.002
- ^ Zheng, C. and Wang, P.P., 1999. MT3DMS: A Modular Three-Dimensional Multispecies Transport Model for Simulation of Advection, Dispersion, and Chemical Reactions of Contaminants in Groundwater Systems; Documentation and User’s Guide. Contract Report SERDP-99-1 U.S. Army Engineer Research and Development Center, Vicksburg, MS. User’s Guide.pdf MT3DMS website
- ^ Chapman, S.W., Parker, B.L., Sale, T.C., Doner, L.A., 2012. Testing high resolution numerical models for analysis of contaminant storage and release from low permeability zones. Journal of Contaminant Hydrology, 136, pp. 106-116. DOI: 10.1016/j.jconhyd.2012.04.006
- ^ Farhat, S.K., Adamson, D.T., Gavaskar, A.R., Lee, S.A., Falta, R.W. and Newell, C.J., 2020. Vertical Discretization Impact in Numerical Modeling of Matrix Diffusion in Contaminated Groundwater. Groundwater Monitoring and Remediation, 40(2), pp. 52-64. DOI: 10.1111/gwmr.12373
- ^ Carey, G.R., Chapman, S.W., Parker, B.L. and McGregor, R., 2015. Application of an Adapted Version of MT3DMS for Modeling Back‐Diffusion Remediation Timeframes. Remediation, 25(4), pp. 55-79. DOI: 10.1002/rem.21440
See Also
- Matrix Diffusion Movie
- Impact of Clay-DNAPL Interactions on Transport and Storage of Chlorinated Solvents in Low Permeability Zones
- Prediction of Groundwater Quality Improvement Down-Gradient of In Situ Permeable Treatment Barriers and Fully Remediated Source Zones
- Determining Source Attenuation History to Support Closure by Natural Attenuation
- Coursera Matrix Diffusion Online Lecture